28 livres d'innovation : Comment ModCribs change la donne pour les équipes de décors modulaires avec ModCribs [transcription du podcast].
28 livres d'innovation : Comment ModCribs change la donne pour les équipes de décors modulaires w/ ModCribs
Scott Bridger, cofondateur de ProSet Modular, présente sa nouvelle entreprise : ModCribs. Quasiment indestructibles et ne pesant que 28 livres chacune, les unités de criblage modulaires ModCribs apportent facilité et efficacité aux fabricants de modules et aux équipes de tournage. Dans cet épisode, Scott décrit l'évolution et les avantages du produit lui-même, explique comment les acteurs d'un projet peuvent l'utiliser sur leur chantier et se penche sur les meilleures pratiques en matière de montage modulaire et de logistique sur site.
John McMullen
Bonjour et bienvenue à Inside Modular : Le podcast de la construction modulaire commerciale, présenté par le Modular Building Institute.
Bonjour à tous. Je m'appelle John McMullen. Je suis le directeur du marketing chez MBI. Aujourd'hui, j'ai le plaisir d'accueillir Scott Bridger, cofondateur de ProSet Modular et désormais cofondateur de ModCribs. Scott est ici aujourd'hui pour parler du développement de ModCribs et de ce que ce produit pourrait signifier pour l'industrie.
Scott, merci d'être ici.
Scott Bridger
Merci de m'accueillir, John. Je me réjouis de cette conversation.
John McMullen
Tout le plaisir est pour moi. Alors, plongeons dans le vif du sujet. En tant que l'un des dirigeants de ProSet depuis longtemps, vous avez pratiquement tout vu en matière de construction modulaire et de mise en place modulaire. Quel est ce processus en quelques mots ? Pourquoi le montage et la logistique sur site sont-ils si importants pour un projet modulaire ?
Scott Bridger
C'est une question assez vaste, mais très pertinente. Je pense que je devrais commencer par dire que notre société, ProSet, et maintenant ModCribs, se concentre essentiellement sur le monde modulaire et ce que nous appelons le modulaire commercial, et même plus spécifiquement, les projets multifamiliaux, d'hospitalité, d'aide à la vie autonome, ce type de projets. Comme vous le savez, les projets modulaires commerciaux constituent un vaste ensemble, mais c'est en quelque sorte la base de notre activité dans l'industrie. C'est donc dans ce cadre que s'inscrivent les types de projets auxquels nous nous référons et sur lesquels nous travaillons. Essentiellement, la logistique est assez compliquée, simplement en raison de la portée et de la taille de beaucoup de ces projets. Ainsi, le projet d'installation moyen de ProSet est d'environ 100 unités modulaires, généralement dans un seul bâtiment, mais il peut s'agir de plusieurs bâtiments.
Nos projets peuvent aller de 20 ou 30 unités modulaires jusqu'à 400, 500 unités modulaires ou plus. La fourchette est donc large, mais le fait est qu'il s'agit de projets assez complexes lorsqu'il s'agit de planifier la logistique telle que vous la décrivez. La logistique associée au champ d'action de ProSet correspond en fait à ce que nous pensons à partir du moment où une unité modulaire quitte l'usine où elle a été produite, jusqu'à ce qu'elle soit fixée de manière permanente et sûre à une fondation. C'est donc le cycle de vie dans lequel nous vivons et où cette logistique devient critique. Nous verrons certainement comment ModCribs joue un rôle à cet égard. Cela commence en quelque sorte par l'ordre dans lequel nous allons installer un bâtiment, car chaque unité modulaire a son espace spécifique dans le bâtiment, elles ne sont pas interchangeables. Nous créons donc un ordre précis basé sur la logistique des grues, les conditions du site et toutes sortes de conditions, l'ingénierie structurelle, les détails, etc. L'ordre dans lequel nous allons placer le bâtiment détermine toute la logistique du processus. Il nous indique l'ordre dans lequel nous devons les recevoir de l'usine ou d'une aire de stockage locale, ce qui détermine l'ordre dans lequel ils doivent être expédiés par la société de transport, qui indique généralement au fabricant l'ordre dans lequel il les construira. C'est donc l'ensemble de ce processus que nous considérons comme la logistique préétablie.
John McMullen
Pouvez-vous me présenter tous les éléments physiques nécessaires à la réussite d'un projet ? Je sais qu'il y a une grue et de nombreux camions. Mais à part cela, qu'est-ce qui est vraiment nécessaire pour réussir la construction d'un bâtiment modulaire ?
Scott Bridger
La façon la plus simple de décrire cela est donc de suivre le parcours d'une unité modulaire, pour ainsi dire depuis l'usine de fabrication. Mais avant de commencer, je vais commencer par dire que la plupart de ces projets, comme je l'ai décrit avec un nombre assez important d'unités modulaires, vont avoir besoin d'un parc de stockage sur le chantier ou à proximité du chantier. C'est un élément important de cette conversation sur la logistique, car pour beaucoup de personnes qui n'ont peut-être pas vraiment approfondi ce processus, c'est parfois une pièce du puzzle qui n'est pas comprise. La raison pour laquelle nous avons généralement besoin d'un parc de stockage sur le site ou à proximité du chantier est que la plupart des projets sont trop éloignés de l'usine de fabrication pour que l'on puisse simplement prendre une unité modulaire, la mettre sur une remorque et la faire livrer par camion directement à une grue et l'installer sur une fondation. Pour plusieurs raisons, cela fonctionne rarement. C'est ce qu'on appelle la livraison juste à temps. C'est une pratique que nous déconseillons vivement, car elle est rarement couronnée de succès. La raison principale est que si vous imaginez le temps qu'il faut pour livrer une unité modulaire d'une usine à un chantier ou à un lieu de stockage, un chantier ordinaire, cela représente souvent des centaines et des centaines de kilomètres. Chaque livraison par camion prend donc un jour ou quelques jours.
Ainsi, si 100 unités modulaires sont livrées d'une usine à une aire de stockage située à des centaines de kilomètres, il faudra probablement compter plusieurs semaines de livraison. Les unités modulaires sont livrées au compte-gouttes à cet entrepôt. Lorsque ProSet ou une entreprise comme ProSet commence à installer un bâtiment, ces unités modulaires sont installées à un rythme beaucoup plus rapide. Elles seront installées au moins une dizaine par jour et parfois jusqu'à 20 par jour. C'est beaucoup plus rapide que le processus de transport par camion. C'est pourquoi il est nécessaire de disposer d'un parc de stockage local.
Revenons en arrière et passons rapidement en revue le processus, du berceau à la tombe, pour ainsi dire de la livraison aux fondations. Une unité modulaire est achevée dans une usine. En général, l'usine dispose d'un parc d'entreposage extérieur sur son site et stocke certaines de ces unités modulaires avant qu'elles ne soient expédiées sur le chantier. Elle va laisser le stock de ces unités s'accumuler pour plusieurs raisons. Il se peut que le chantier ne soit pas prêt, qu'ils veuillent avoir un programme de camionnage efficace afin de ne pas attendre que les unités modulaires soient terminées avant d'en expédier une autre, c'est un moyen plus efficace de laisser certaines unités être terminées. Dans un premier temps, un certain nombre d'unités modulaires sont stockées sur des berceaux dans une usine de fabrication modulaire, puis elles sont transportées par camion de l'usine à l'entrepôt local ou éventuellement sur le site. Le transport sur site n'est pas courant, car la plupart des chantiers ne disposent pas d'un tel espace. Il y a donc généralement un parc de stockage à quelques kilomètres du chantier, si tout va bien. Maintenant que le parc de stockage est rempli de toutes ces unités modulaires, ProSet ou une autre entreprise de construction installe la grue sur le chantier et procède à ce que l'on appelle la navette locale. Une entreprise de camionnage vient alors chercher ces unités modulaires sur le chantier et les livre directement à la grue. En règle générale, elles sont grutées dès leur sortie du camion, sur les fondations, structurellement sécurisées. Et en général, c'est à peu près la fin de notre travail, et nous passons au travail suivant. C'est en quelque sorte le parcours d'une unité modulaire.
John McMullen
J'ai compris. Vous l'avez mentionné dans vos réponses. Oh, eh bien, allons droit au but. Parlez-moi de l'encoffrement. J'ai visité quelques usines et j'ai vu différentes choses utilisées comme cribbing, principalement du bois, mais aussi d'autres matériaux.
Scott Bridger
Bien sûr. Je pense que tout commence par la réponse à votre question : qu'est-ce que le cribbing ? Pourquoi est-il nécessaire et comment est-il utilisé ? Nous pourrons ensuite aborder les détails des différents types de cribbing. Le cribbing est essentiellement un support temporaire pour les unités modulaires volumétriques. Passons donc en revue les différents types de supports. Commençons par la partie temporaire. Lorsque j'ai décrit le parcours d'une unité modulaire, de l'usine aux fondations, il y a plusieurs arrêts en cours de route. La première étape est probablement l'entreposage sur le chantier du fabricant. L'unité doit être soutenue temporairement, que ce soit pour un jour, une semaine ou un mois, ou pour une durée quelconque. Il doit être soutenu temporairement avant d'être transporté vers le parc de stockage. Une fois qu'il est arrivé au parc de stockage, il doit à nouveau être soutenu temporairement. Le plus souvent, ces unités modulaires ne sont donc pas conçues pour être posées directement sur le sol. Cela s'explique en partie par un élément important de la logistique et du transport des unités modulaires, à savoir la manière dont elles sont placées sur les remorques et en sont retirées. La norme dans l'industrie, qui est devenue très efficace et très courante, veut que les unités soient transportées sur des remorques hydrauliques ou aériennes qui peuvent se soulever et s'abaisser. Il s'agit là d'un élément très important de l'encoffrement. La raison pour laquelle le cribbing est si efficace et abordable dans le grand schéma de cette logistique est que le cribbing et ces remorques réglables éliminent la nécessité de charger et de décharger les unités modulaires à l'aide d'une grue.
Les grues sont très coûteuses. Tout d'abord, l'unité modulaire doit être soulevée et placée sur une remorque dans l'usine pour être tirée hors de l'usine. Elle doit ensuite être soutenue par des berceaux, puis la remorque s'abaisse et se retire sous l'unité modulaire. Lorsque l'unité modulaire doit quitter le parc de stockage de l'usine pour être transportée sur le chantier local, une remorque revient sous l'unité modulaire, la soulève des berceaux et la transporte sur des centaines de kilomètres jusqu'au parc de stockage du chantier. Une fois de plus, on place les berceaux sous l'unité modulaire, on fait descendre la remorque de dessous l'unité modulaire, et c'est ainsi qu'elle reste sur le site de stockage. Pour la dernière étape de son voyage, une remorque revient sous l'unité modulaire dans le parc de stockage, la soulève des berceaux et la livre à la grue.
Si l'on considère les choses sous cet angle, le cribbing n'est qu'un support temporaire pour les unités modulaires afin que les remorques puissent passer sous l'unité modulaire et la soulever et l'abaisser sans avoir besoin d'une grue. C'est en quelque sorte la raison pour laquelle les cribs sont nécessaires. Les remorques typiques dont nous parlons se lèvent et s'abaissent généralement de 32 à 42 pouces. C'est en quelque sorte la plage qu'ils peuvent abaisser et soulever. Nous avons donc construit nos modcribs, la plupart des berceaux en bois et les autres berceaux de l'industrie mesurent 36 pouces de haut, parce que c'est un peu le juste milieu. C'est donc à peu près ce qu'est un lit d'enfant dans l'industrie modulaire commerciale. En ce qui concerne les types de lits d'enfant. La plupart des berceaux utilisés aujourd'hui et dans le passé sont simplement constitués d'une pile de deux par quatre. C'est aussi simple que cela. Pour construire un berceau en bois, il faut en moyenne douze deux par quatre et environ 400 clous. L'unité modulaire moyenne a besoin de huit ou dix berceaux pour la soutenir. Donc, comme vous pouvez l'imaginer, si vous commencez à faire le calcul pour cent unités modulaires, un nombre extraordinaire de clous et de deux par quatre, ils sont lourds, ils sont difficiles à transporter et ils ne résistent pas très longtemps aux intempéries. Il y a donc beaucoup de choses qui font que les berceaux en bois ne sont pas très efficaces. L'autre méthode que nous avons vue, ou les autres matériaux que nous avons vus, c'est que quelques usines ont fabriqué leurs propres berceaux pour les utiliser dans leurs cours d'usine et ils sont généralement en acier. Nous avons vu quelques fabricants créer leurs propres berceaux en acier. Lorsque les berceaux ne sont pas déplacés d'un chantier à l'autre, il n'est pas aussi important qu'ils soient légers, empilables et faciles à transporter. Ainsi, les berceaux en acier que certaines usines de fabrication utilisent pour leur propre usage sur leur chantier ne répondent à aucun de ces critères. Ils ne sont pas empilables, ils ne sont pas légers, ils ne sont pas faciles à transporter et ils ne sont pas abordables. Mais s'il s'agit d'une solution permanente pour le chantier de l'usine, ces éléments ne sont peut-être pas aussi importants. En revanche, il est important qu'ils soient légers, empilables, durables et faciles à transporter lorsqu'il s'agit de les déplacer d'un chantier à l'autre dans la campagne. C'est là que nous avons vu un besoin et que nous avons développé ModCribs.
John McMullen
Parlez-moi donc de ModCribs. Comment ce produit a-t-il été développé ? Il est évident que vous avez vu beaucoup de types de lits d'enfant différents, fabriqués avec beaucoup de types de matériaux différents et de différentes manières. Avez-vous eu une sorte d'illumination ou la gestation de l'idée a-t-elle été plus lente ?
Lire aussi :
Les ModCribs sont une meilleure solution
Scott Bridger et Matt Mitchell, cofondateurs de ProSet Modular, ont tout vu en matière d'encorbellements modulaires, tout en prenant des notes sur la manière de les améliorer. Finalement, "nous nous sommes dit qu'il ne semblait pas que quelqu'un travaille vraiment à une meilleure solution", a déclaré M. Bridger. C'est à ce moment-là, il y a environ quatre ans, qu'ils ont décidé de voir ce qu'ils pouvaient faire. "C'est à ce moment-là que nous avons vraiment décidé de voir si nous pouvions concevoir et fabriquer quelque chose de meilleur", a déclaré M. Mitchell.
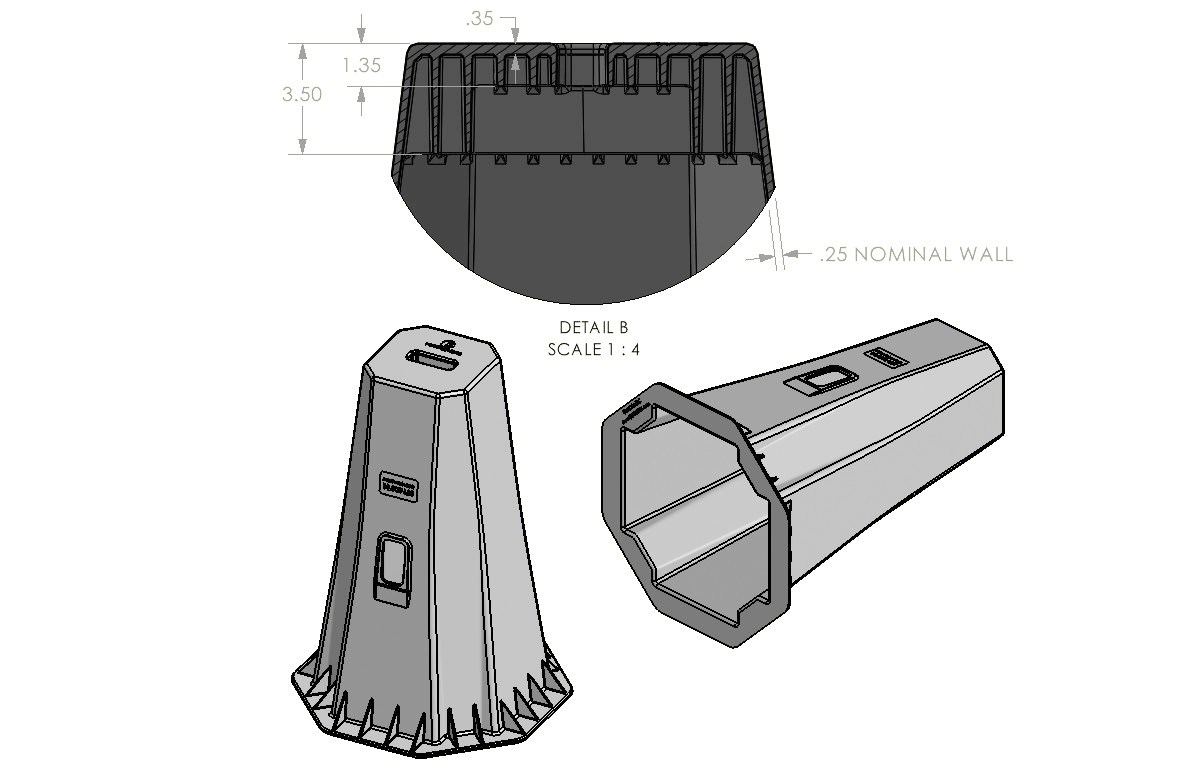
Scott Bridger
Croyez-le ou non, c'est un peu les deux. Je suis dans le secteur depuis longtemps et mon partenaire Matt Mitchell y est depuis bien plus longtemps que moi. Il y travaille depuis trois décennies et moi depuis une seule. Néanmoins, après avoir eu de très nombreuses conversations au fil des ans sur les problèmes que posent les lits d'enfant en bois, j'ai décidé de me lancer dans l'aventure. Je ne parle pas de conversations internes à ProSet, mais de conversations à l'échelle de l'industrie. Je veux dire, à l'échelle de l'industrie. Les lits d'enfant ont toujours été un aspect très pénible de l'industrie et, à notre avis, pendant toutes ces années, tout le monde s'en est plaint et n'a pas voulu en faire partie. Les fabricants ne veulent pas avoir à s'occuper de l'encoffrement, en particulier de l'encoffrement hors site, dans les parcs de stockage pour les clients à proximité du chantier. Les fabricants ne veulent pas avoir à trouver le moyen de faire transporter des cribs en bois lourds, coûteux et encombrants à travers le pays. Ensuite, que fait-on d'eux une fois qu'ils sont terminés sur le chantier et qu'ils sont déplacés vers un autre chantier ou renvoyés à l'usine ? C'est un vrai casse-tête. Au cours des six ou huit premières années de la vie de ProSet, à partir de 2014, c'est ainsi que la conversation s'est déroulée. Ces berceaux sont un vrai casse-tête. Matt et moi en avons parlé au fil des ans et nous avons toujours eu de petites conversations ici et là sur le fait qu'il devait y avoir une meilleure façon de faire.
Nous avons vraiment commencé à faire attention et à essayer de voir ce que les autres faisaient, ce que les différents fabricants faisaient. Il existait de légères variantes de berceaux en bois. Certains sont un peu plus grands, d'autres un peu plus petits, certains ont plus de bois, d'autres moins, mais c'est plus ou moins la même chose. Il s'agissait simplement de piles de deux par quatre, comme je l'ai décrit. Ensuite, il y avait quelques usines qui, comme je l'ai mentionné, construisaient leurs propres structures en acier. Nous étions au courant de leur existence et nous avons eu l'occasion d'essayer d'en soulever quelques-uns, mais nous savions que ce n'était pas la solution. À un moment donné, nous avons rendu visite à un fabricant, il y a environ quatre ans, et ce fabricant, dont je ne citerai pas les noms, utilisait dans ses installations des berceaux et des caissons en bois extrêmement lourds et encombrants. Il faut probablement un chariot élévateur pour déplacer un seul berceau. En voyant cela, nous n'avons rien dit à l'usine ni l'un à l'autre au cours de la visite. Lorsque nous sommes rentrés chez nous après cette visite, nous avons tous les deux fait des commentaires sur ce berceau. C'est à ce moment-là que nous nous sommes dit que ça suffisait, qu'il fallait que quelqu'un trouve une solution. Nous nous sommes donc mis au travail, en essayant vraiment de trouver une solution. Je peux vous donner un aperçu du déroulement de cette réflexion et de la façon dont le produit a finalement été développé.
Ce n'était pas très efficace, ni très rapide. À l'origine, nous nous sommes demandé comment définir les critères. Il faut qu'il soit léger, empilable, durable, qu'il supporte le poids et dure longtemps. Enfin, le dernier critère, qui est lui aussi assez difficile, est qu'il doit être abordable, parce qu'il y en a beaucoup qui sont nécessaires. Les berceaux en bois ne sont pas terriblement chers et s'ils ne sont pas relativement abordables, ils ne seront probablement pas largement acceptés. Voilà donc nos principaux critères. Léger, empilable, durable et abordable. Nous avons cherché ce que nous pouvions trouver et nous avons d'abord pensé que l'aluminium répondrait à ces critères. C'était parfait pour la légèreté, l'empilabilité et la durabilité, mais quand il s'est agi de trouver un produit abordable, ce n'était pas du tout le cas. C'était beaucoup trop cher. Nous avons donc ébauché un projet et Matt en a fait une maquette en Masonite dans son garage. C'est là que tout a commencé et nous l'avons encore aujourd'hui. Je pense qu'un jour, elle fera partie du musée ModCribs.
Nous avons donc pensé que l'aluminium fonctionnerait, nous avons travaillé avec un ingénieur, nous avons essayé d'obtenir des prix et nous avons réalisé que ce n'était pas une bonne idée, simplement à cause du coût. Finalement, un ingénieur avec lequel nous travaillions nous a proposé l'idée de la mousse structurelle, qui est essentiellement du plastique structurel, ce qui nous a semblé un peu étrange parce que nous n'y avions pas pensé et nous a semblé assez étonnant qu'il soit possible de créer un berceau qui réponde à ces critères à partir de plastique. Nous avons donc commencé à travailler sur ce concept et c'est essentiellement ce que nous avons obtenu. Il s'agit d'un polypropylène moulé par injection avec un peu de fibre de verre. Nous en sommes maintenant aux essais finaux et au produit final, qui a été testé à merveille. Il a passé les tests de charge avec brio. En fait, il y a un facteur de sécurité six fois supérieur à ce qui est prévu. Il est donc extrêmement solide et peut supporter beaucoup plus de poids que nécessaire. Il est empilable, léger et très rentable. Il n'est pas beaucoup plus cher qu'un berceau en bois. Voilà où nous en sommes aujourd'hui.
John McMullen
C'est fantastique. Scott, merci beaucoup. Vous avez répondu à un grand nombre de mes questions. L'autre jour, j'étais sur LinkedIn et j'ai vu un commentaire de nos amis de Stream Modular. Ils ont dit que les ModCribs allaient changer la donne, ce qui m'a vraiment frappé et m'a enthousiasmé. Quels autres commentaires avez-vous reçus de la part de ceux qui ont utilisé ModCribs ? Quel a été l'accueil jusqu'à présent ?
Scott Bridger
Eh bien, c'est très amusant et les réactions sont très positives. Ce n'est pas inattendu, parce que ProSet et son personnel ont été en première ligne pour relever les défis des berceaux en bois, comme n'importe qui d'autre. Nos équipes sont sur le terrain et doivent déplacer ces lourds berceaux en bois par centaines, voire par milliers, sur un chantier. Nous savons donc à quel point les ModCribs sont plus conviviaux et plus efficaces que les cribs en bois. Ce n'est donc pas inattendu, mais c'est toujours très amusant et excitant de recevoir ces réponses. Carson et l'équipe de Stream nous ont beaucoup soutenus et se sont montrés très enthousiastes. Ce n'est pas non plus une surprise, car les chauffeurs de camion qui effectuent les livraisons de ces unités modulaires sont aussi ceux qui vont bénéficier grandement de cette initiative, car ils ont aussi pour tâche de traîner ces berceaux en bois. Les équipes de montage, les équipes de camionnage, les employés des usines de fabrication qui doivent travailler avec les caissons en bois. Tous ces gens sont ravis à l'idée de remplacer les berceaux en bois par des ModCribs, surtout lorsqu'ils ont l'occasion de mettre la main sur un ModCrib. C'est donc très amusant.
Nous avons fait quelques tournées dans les principales usines de fabrication du pays et nous avons apporté quelques échantillons de ModCribs pour qu'ils puissent les prendre en main et les voir. Chaque fois qu'ils les prennent par la poignée, ils sourient. En réalité, les 28 livres que pèsent ces ModCribs sont un tel soulagement par rapport aux 100 livres et plus de certains berceaux en bois que nous avons vus peser jusqu'à 200 livres. Selon les normes de l'OSHA, c'est bien plus que ce qu'un travailleur individuel devrait essayer de soulever. Je crois que l'OSHA stipule qu'il ne faut jamais demander à un seul travailleur de soulever plus de 50 livres. Ainsi, le simple facteur de sécurité et la réduction de la charge de travail des personnes chargées de manipuler les lits d'enfant ont un impact considérable. Je pense que c'est en grande partie ce que Stream a commenté en termes de changement de la donne. De nombreuses usines sont très enthousiastes à l'idée de remplacer leurs berceaux en bois par des ModCribs, ne serait-ce que pour cette raison, parce qu'elles se soucient vraiment du bien-être de leur personnel et de leurs employés. Elles se rendent compte que cela va alléger le fardeau humain que représentent les berceaux en bois. C'est donc très amusant.
Je pense que l'autre élément du commentaire de Carson qui change la donne, en particulier celui de Stream, du point de vue du camionnage, c'est que les ModCribs sont empilables. Vous pouvez transporter beaucoup, beaucoup, beaucoup plus de ModCribs sur un seul chargement de camion que vous ne pouvez le faire avec des berceaux en bois. En fait, je pense que, grosso modo, nous pouvons transporter environ 1 200 ModCribs dans un semi-remorque, contre 250 à 300 cribs en bois. Cela réduit donc les trajets en camion. Par exemple, si vous avez un projet de 1200 berceaux, ce qui pourrait ne représenter que 120 unités modulaires, ce n'est pas un projet énorme. C'est un travail assez moyen. Par conséquent, si l'on considère le volume de berceaux requis dans ces parcs de stockage, il est considérable. En moyenne, disons 100 ou 120 projets modulaires, cela signifie que la livraison de cribs de bois pour soutenir ces unités va nécessiter quatre ou cinq chargements de semi-remorques, ce qui représente beaucoup de dépenses. Cela représente beaucoup de carburant, des impacts sur l'environnement, beaucoup de temps et de manutention. Imaginez donc que vous ayez quatre ou cinq semi-remorques remplis de ces lourds berceaux en bois, comment les décharger ? Il faut un chariot élévateur. Il faut ensuite les disperser tout autour du parc de stockage pour qu'ils ne soient pas trop éloignés de l'endroit où les chauffeurs de camion vont livrer les modules et que ces derniers soient obligés de les traîner partout pour que quelqu'un les répartisse dans le parc de stockage. C'est une tâche lourde et coûteuse, contrairement aux ModCribs que l'on peut littéralement transporter deux par deux. Je pense donc que ce sont là les éléments qui changent la donne. C'est vraiment une question de facilité d'utilisation et de transport.
John McMullen
On dirait que vous allez vous faire beaucoup d'amis dans le secteur. Je me sens mal pour les chiropracteurs parce que tu leur enlèves beaucoup de travail !
Scott Bridger
Je ne vais pas me sentir mal.
John McMullen
Vous avez été sur la route avec ces produits. J'ai vu sur LinkedIn que vous avez participé à plusieurs expositions et que vous avez visité de nombreuses usines. Où quelqu'un peut-il voir ModCribs prochainement s'il est enthousiaste à l'idée d'approcher de près l'un de ces produits ?
Scott Bridger
Il y a plusieurs façons de procéder. Évidemment, quiconque souhaite voyager un peu est invité à venir les voir sur l'un des chantiers où nous les utilisons. Comme vous l'avez dit, nous voyageons aussi beaucoup. Mon partenaire Matt et moi-même parcourons chaque année de nombreux kilomètres à travers le pays. Nous nous rendons tous les deux sur nos chantiers et chez les fabricants du pays. Nous passons donc beaucoup de temps à visiter des usines dans différentes régions du pays. Nous sommes heureux de rendre visite à toute usine intéressée et de lui apporter des échantillons. L'autre chose que je dois souligner, c'est que ModCribs est une entreprise de location à court terme de ModCribs dans les parcs de stockage, comme je l'ai décrit, et je vais peut-être prendre de l'avance si vous posez cette question. C'est une entreprise de location. Nous avons cependant un programme limité de vente en gros, exclusivement destiné aux fabricants, pour qu'ils l'utilisent dans leurs parcs d'entreposage. Nous voulons donc que les usines aient la possibilité de les utiliser dans leurs installations, comme je l'ai décrit plus tôt, pour soulager leurs employés. Il s'agit d'une option beaucoup plus efficace pour leur personnel. Nous ne voulons donc pas limiter la capacité des usines à les utiliser. Cela n'aurait pas de sens pour elles de les louer parce qu'elles en ont besoin toute l'année. Nous avons donc un programme de vente réservé aux usines. Essentiellement, notre modèle d'entreprise consiste à louer ces produits aux promoteurs et aux GC dans les zones de stockage temporaire à travers le pays.
John McMullen
Très bien. Très bien. Et oui, vous avez répondu à une question avant que je puisse la poser, mais ce n'est pas grave. Scott, vous avez parlé de l'aspect location de votre activité, vous avez parlé des ventes que vous proposez aux fabricants. Comment cela fonctionne-t-il ?
Scott Bridger
Merci pour cette question. C'est une autre raison pour laquelle Matt et moi avons pris la décision, il y a quelques années, d'améliorer et d'aider à résoudre ce problème difficile qu'est le cribbing. Ce n'est pas seulement parce que les berceaux en bois sont encombrants, chers, qu'ils se dégradent sous l'effet des intempéries, etc. C'est aussi parce que les caissons sont temporaires. Les exigences en matière d'encoffrement dans les parcs de stockage sont souvent négligées, car elles ne sont pas prises en compte par les différentes parties prenantes. Par exemple, lorsque le promoteur envisage tous ses coûts et tous les contrats qu'il doit conclure pour achever son bâtiment, il dispose de toutes les pièces du puzzle. Il va passer un contrat avec le fabricant, un contrat avec un entrepreneur général, et probablement un contrat avec une entreprise de camionnage. Ainsi, dans tout ce processus, la pièce du puzzle que sont les berceaux temporaires dans un parc de stockage, pour quelque raison que ce soit, est très souvent oubliée. Je pense que cela fait partie de l'histoire globale des berceaux et de la raison pour laquelle nous avons créé ModCribs, à savoir que ce type de berceau n'entre pas vraiment dans le champ d'action de qui que ce soit.
En général, l'entrepreneur général est au courant ou y pense. Pour le fabricant, c'est un peu en dehors de son champ d'action, car une fois que les unités modulaires quittent l'usine, son champ d'action est pratiquement terminé. Enfin, l'entreprise de camionnage en est consciente, mais elle n'intervient généralement que tardivement dans la conversation. Pour toutes ces raisons, il arrive souvent que l'on ne tienne pas compte du budget, de la planification, du champ d'application et de l'identité de l'entreprise. Ce que ModCribs propose, et je pense que cela va contribuer à atténuer cette sorte de pièce manquante du puzzle, c'est tout d'abord de sensibiliser l'industrie au besoin et à l'opportunité que ModCribs apporte à ce processus. En même temps, nous créons ce que nous considérons comme un bouton facile à utiliser pour le développeur. En fin de compte, c'est souvent le promoteur qui se retrouve coincé et qui doit trouver un moyen d'acheminer les lits d'enfant dans son parc de stockage, souvent à la dernière minute, parce que personne ne l'avait prévu et qu'on l'a tout simplement oublié.
Historiquement, nous avons eu de nombreux projets sur lesquels ProSet a travaillé où l'entrepreneur général devait se démener et envoyer quelques charpentiers dans la cour de stockage avec un tas de deux par quatre et essayer de construire rapidement 1000 de ces berceaux. Ce n'est pas rare. Le bouton facile que nous avons créé avec ModCribs est un processus simple qui consiste à contacter ModCribs, à nous indiquer le nombre d'unités modulaires dont vous avez besoin, où se trouve la cour de stockage et quand vous devez commencer à recevoir ces unités modulaires. Nous vous fournirons un devis et nous vous aiderons à déterminer le nombre de berceaux dont vous avez besoin. En règle générale, le devis est établi pour une durée maximale de 60 jours, car c'est normalement la durée pendant laquelle le projet aura besoin de ces berceaux temporaires. Une fois le contrat exécuté, nous livrons ces berceaux avant que les unités modulaires ne commencent à arriver. Dès que la dernière unité modulaire est installée sur les fondations, le client peut nous appeler et nous venons les chercher. Cela simplifie vraiment tout le processus.
Cela permet également d'éviter le problème que nous rencontrons avec les berceaux en bois qui, historiquement, revient à cet exemple où personne n'a pensé aux berceaux et où les entrepreneurs généraux se sont empressés de construire tous ces berceaux en bois. C'est un processus coûteux en temps et en énergie, mais que se passe-t-il à la fin ? Tous les bâtiments sont maintenant installés et je peux vous montrer d'innombrables photos de ce à quoi ressemble ce parc de stockage lorsque la dernière unité modulaire est installée. Il y a des berceaux en bois lourds et éparpillés dans toute la cour. Il faut maintenant les rassembler, les recréer, les mettre dans un camion et les transporter quelque part. Malheureusement, dans de nombreux cas, ce processus est si coûteux qu'ils ne sont jamais réutilisés. Ils sont jetés parce que c'est moins coûteux que d'essayer de trouver un moyen de les transporter et de les stocker quelque part. C'est pourquoi le fait d'éliminer ce processus inefficace et difficile pour l'industrie est, je pense, l'un des grands changements apportés par ModCribs.
John McMullen
Il s'agit d'un véritable microcosme de l'ensemble de l'industrie de la construction modulaire. Si vous y réfléchissez, c'est plus efficace, plus durable. C'est plus rapide.
Scott Bridger
Vous avez tout à fait raison. L'autre aspect amusant de la question est de savoir ce qu'est la modularité. Qu'est-ce que l'industrie modulaire ? Il s'agit vraiment d'innovation, n'est-ce pas ? En tant qu'industrie, nous innovons dans la façon dont nous construisons les bâtiments commerciaux aux États-Unis. ModCribs est un produit de très faible technicité, mais nous aimons à penser qu'il est un peu innovant parce qu'il répond à un besoin du secteur.
John McMullen
Alors, ModCribs mis à part, quelles autres avancées ou innovations pensez-vous que l'industrie puisse attendre avec impatience en matière de logistique de mise en place et de logistique sur site ?
Scott Bridger
Oh, c'est une bonne question. La réponse sera peut-être un peu étrange. De mon point de vue, en tant que personne qui travaille dans le domaine de l'installation depuis un certain temps, je pense que ce que nous voyons, c'est un progrès dans le processus, je dirais. Il y a certainement des technologies et des conceptions de plus en plus performantes en termes d'équipement. En fait, mon partenaire Matt et Chris Rimes, l'autre propriétaire de notre entreprise, ont mis au point nos halos personnalisés. C'est quelque chose qui a ajouté beaucoup d'efficacité à notre processus d'installation parce qu'ils sont très flexibles et ajustables. C'est un équipement vraiment génial. Ce sont donc des choses que nous voyons progresser en termes d'équipement, et ainsi de suite sur le site. Je pense que nos équipes s'améliorent constamment dans la mise en œuvre de la logistique, des plans, des systèmes et des processus qui nous permettent d'installer ces bâtiments de manière plus efficace. Je pense qu'il s'agit avant tout de continuer à améliorer le processus. Toute la logistique du berceau que j'ai décrite aboutit en fin de compte à ce qu'une grue soulève une unité modulaire et la pose sur nos fondations. C'est en quelque sorte la dernière étape de ce processus, mais l'efficacité du nombre d'unités modulaires que la grue peut prendre et poser sur une fondation à un moment donné dépend de la planification, de la logistique, de la coordination générale et de la programmation du processus. Je pense donc que c'est là que je vois des progrès continus. Nous en avons la preuve concrète, car nous travaillons beaucoup, en examinant les données historiques de nos projets. Nous constatons des augmentations significatives de notre efficacité et du nombre d'unités modulaires moyennes par jour que nous avons fixé il y a deux ou trois ans. C'est sur ces progrès que nous allons continuer à travailler.
John McMullen
En parlant d'innovation, je suis heureux que vous en ayez parlé. Je tiens également à vous remercier pour l'interview que vous avez accordée récemment à MBI. ModCribs fait l'objet d'un article dans le numéro de novembre-décembre du magazine Modular Advantage. Je vous remercie donc pour le temps que vous y avez consacré et pour le temps que vous nous avez accordé pour cette interview, Scott. Je vous en suis très reconnaissant.
Scott Bridger
Je vous remercie, John. J'apprécie que vous m'ayez invité à l'émission.
John McMullen
Je m'appelle John McMullen. Voici un nouvel épisode d'Inside Modular : Le podcast de la construction modulaire commerciale. Jusqu'à la prochaine fois.